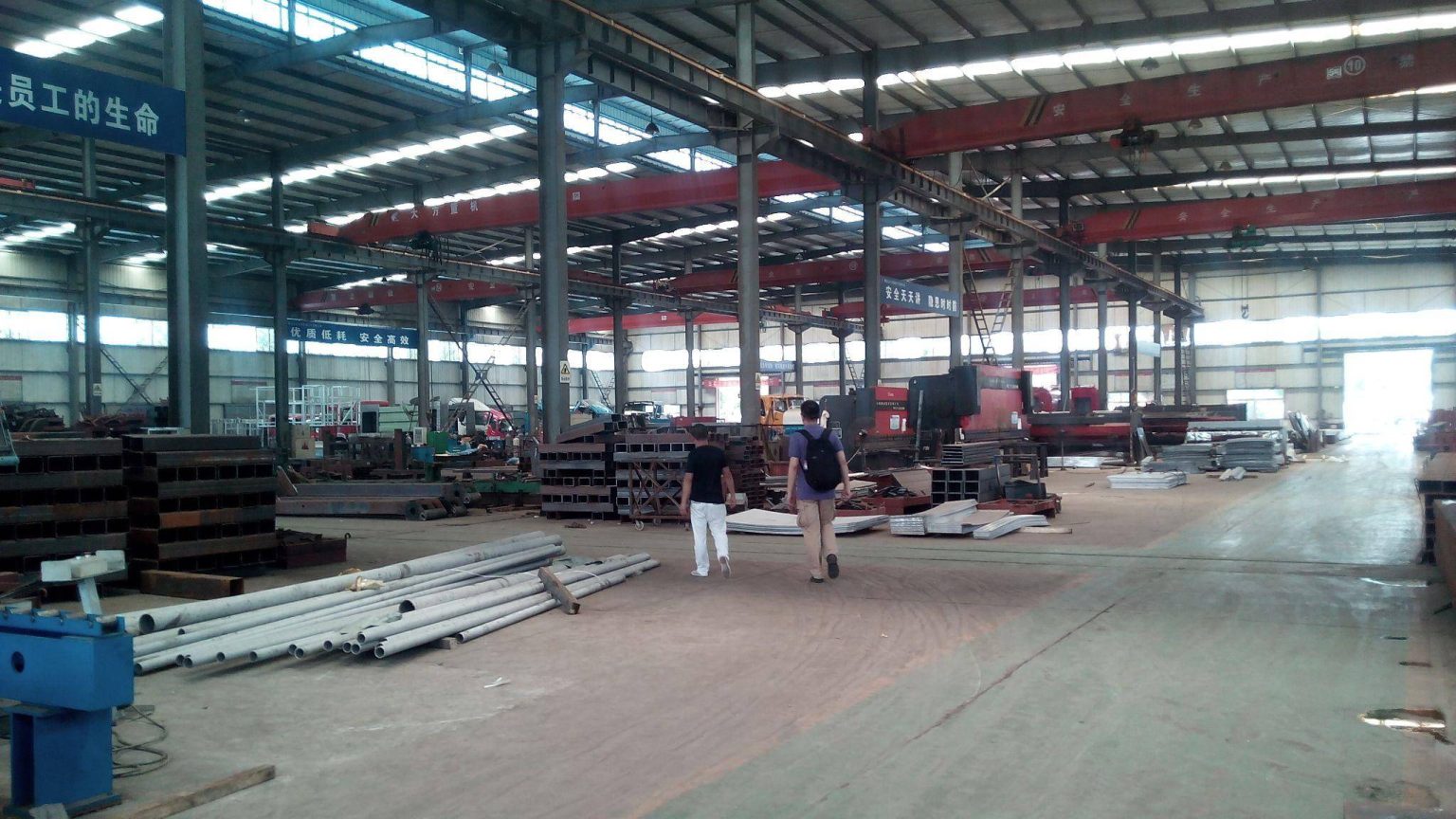
When working with a new supplier, it is important for business owners to consider the potential risks involved. This includes verifying the legitimacy of the supplier’s business and ensuring that they are able to meet your quality standards. One effective method to assess new suppliers is through factory audit services.
Gain insight into the scope of general third-party factory audits for industrial goods and their risk reduction capabilities.
What is a China Factory Audit?
A third-party factory audit in China offers a thorough assessment of a supplier capabilities in comparison to supplier audits. These audits primarily revolve around confirming that the supplier meets legal requirements and has the capacity to consistently produce goods that meet your quality standards. Independent third-party quality control companies typically conduct these audits.
Why are Third-Party Factory Audits Important?
Third-party factory audits are essential for verifying a supplier ability to consistently meet quality standards. They serve as a crucial step in evaluating a vendor’s quality and provide an unbiased assessment of their capabilities. These audits also identify potential risks and may offer recommendations for corrective actions.
Through a factory audit, your company can confidently assess the supplier reliability and ability to meet your quality standards.
When evaluating a factory, businesses must ensure their manufacturing partners meet high standards of quality, efficiency, and compliance. At Eagle Eyes, we have a straightforward process that helps our clients avoid risks and achieve the best possible results. Let us take a step-by-step look at our factory evaluation method.
Step 1: Pre-Audit Preparation
Modern port equipment at a Central Asian hub.
Prior to visiting a factory, we thoroughly prepare in order to increase our efficiency and productivity. The following are the steps we follow:
Understanding Client Needs
- The merchant suggests communicating with the client to determine their specific needs and requirements from the factory. This could include desired product quality, production volume, and any specific guidelines that must be followed. By understanding these factors, the factory can better meet the client’s expectations.
Document Review
- We analyze the factory’s documentation, which encompasses certifications, operational licenses, and past audit reports. This allows for a comprehensive understanding of the factory’s operations thus far.
Detailed pre-shipment inspection by Eagle Eyes.
Creating a Checklist
- Our factory utilizes a comprehensive checklist to ensure all client requests are met with utmost organization. This efficient system is imperative for maintaining productivity and satisfying customer needs, as it is based solely on objective and factual criteria.
Step 2: Initial On-Site Inspection
On-site inspection from Eagle Eyes’s expert specialists.
The initial factory visit provides crucial insight into its fundamental functions. This assessment aids in identifying priority areas for improvement. While conducting the visit, we analyze:
Raw Materials
- The quality of the products is directly influenced by the materials used and their origin. As a knowledgeable expert in the industry, we thoroughly inspect these materials to ensure their excellence. It is a fact that good raw materials result in superior products, which is why we strive to source only the best materials.
Infrastructure
- Inspect the structures and equipment to ensure their safety and cleanliness. It is crucial to properly maintain and keep the buildings and machines in good working condition.
Eagle Eyes’s experts visit to the steel factory.
Workforce
- Observe the workers and determine the total number of employees, their respective roles, and the level of safety and comfort in their working environment.
Eagle Eyes closely observes the factory workforce in action.
Step 3: Quality Control Assessment
Eagle Eyes’s quality control in caustic soda testing.
The manufacturer ensures that the end product is consistent and meets the expectations of the client through quality control measures. It is crucial to maintain high standards of quality for our products. A reputable factory should have efficient systems in place to assess the quality at every stage of production. Here are the key factors we consider.
Testing Facilities
- Does the factory possess the necessary testing equipment and collaborate with certified testing agencies to ensure that its products meet standards? If not, what steps does it take to ensure quality control?
Processes and Protocols
- The article explores the quality control processes used by the factory during production. Are there established guidelines and procedures in place?
Defect Rates
- As an industry expert, we analyze records to determine the rate of product problems in the past and the effectiveness of the factory’s solutions.
Step 4: Compliance Check
Eagle Eyes ensures laboratories meet strict compliance standards.
Factories must adhere to compliance checks to avoid potential consequences such as fines or shutdowns, which can negatively impact our client’s business. These regulations are in place to promote safety, fair practices, and environmental protection. As a product expert, we prioritize verifying compliance during this step.
Labor Laws
- The treatment of workers is a topic of concern for many, as it is essential to ensure fair compensation and reasonable working hours. To protect the rights of employees, labor laws have been put in place to guarantee respect and fairness in the workplace.
Environmental Compliance
- The manufacturer takes responsibility for managing waste and controlling emissions, with a focus on protecting the environment as a top priority.
Safety Standards
- The factory will be inspected to ensure proper safety equipment is in place, including fire extinguishers and emergency exits. Additionally, all workers are trained to effectively handle any potential emergencies.
Step 5: Production Capacity Evaluation
Assessing production capacity with Eagle Eyes’s expertise.
The manufacturer must meet the needs of their clients by producing efficiently and quickly. This process allows for an understanding of production capabilities and delivery speeds, with a focus on:
Bottleneck Identification
- Are there any delays during the production process? For instance, delays can be caused by a slow machine or a shortage of workers. We are able to identify and address these issues.
Capacity Analysis
- The factory’s production capabilities can be evaluated by measuring the number of products it can manufacture within a day, week, or month. This serves as an indicator of its capacity to fulfill large orders.
Lead Times
- The production timeline, from receiving raw materials to shipping the finished product, can vary depending on the factory’s process.
Step 6: Final Report and Recommendations
The report we provide offers essential information for clients to make informed decisions and assists factories in streamlining their operations. Upon completion of our evaluation, we compile a comprehensive report that encompasses the following:
Actionable Recommendations
- The merchant may suggest optimizing safety measures, such as implementing more thorough training or upgrading machinery.
Findings Summary
- The factory’s strengths are highlighted, such as its excellent quality control and high production capacity. Weaknesses, such as poor maintenance or compliance issues, are also identified.
Client Consultation
- After thoroughly reviewing the report with the client, we assist them in making an informed decision on whether to continue working with the current factory or consider alternative partners based on objective measures and industry expertise.
Why Factory Evaluation Matters
Eagle Eyes takes factory evaluation seriously, ensuring a thorough and reliable process. By partnering with us, clients can trust their manufacturing choices. Factory evaluation is crucial for multiple reasons, such as ensuring quality and efficiency.
Trust and Reliability
- Our evaluation ensures clients can trust factories, leading to strong business relationships.
High-Quality Products
- Quality control checks are crucial in ensuring that our factory produces high-quality products, ultimately benefiting our clients by avoiding any defective goods.
Risk Reduction
- The assessment of factories allows customers to avoid potential issues, such as delays, low-quality products, and legal complications.
The hidden depths of procurement—Eagle Eyes simplifies it for you.
Actionable Recommendations
- Consider implementing improvements such as enhanced safety training or upgraded machinery. These measures can make a significant impact on overall operations and ensure a safer work environment.
By following these steps, CAMAL ensures its clients get high-quality products from reliable factories. Factory evaluations are the first step toward successful partnerships and better business outcomes.
Eagle Eyes Experience
Eagle Eyes has a wealth of experience in offering tailored solutions to various industries. Our focus is facilitating connections between companies and trustworthy suppliers/manufacturers, guaranteeing excellence, productivity, and adherence throughout the process. Whether it involves sourcing materials, assessing factories, or navigating global trade, businesses can depend on CAMAL to help them excel in competitive markets. Our Methodology
Our Approach
Eagle Eyes does not only connect companies with suppliers or manufacturers, but also offers continuous support to address any challenges that may arise.
- Dispute Resolution: Receive expert assistance for any quality, delivery, or compliance concerns.
- Monitoring: Regular check-ins to ensure the supplier or factory continues to meet expectations.
2. Supplier and Factory Selection
Eagle Eyes utilizes an extensive global network of reliable suppliers and factories to connect clients with partners that fulfill their quality, compliance, and capacity requirements.
- Supplier Database: Our database contains carefully selected suppliers and manufacturers.
- Due Diligence: Before matching clients with suppliers, we carefully assess the suppliers to ensure they meet the client’s standards.
3. Client First
The initial step we take is to actively listen. Each business faces distinct obstacles, such as securing top-notch merchandise, locating a dependable production collaborator, or maneuvering through intricate global trade regulations. We dedicate time to comprehend the particular objectives and needs of every customer.
- Customized Solutions: Our customized approaches are crafted based on the specific demands of the industry, product requirements, and standards for excellence.
- Expert Insights: Leveraging our team’s extensive expertise, we assist clients in optimizing their sourcing or production strategies to achieve optimal results.
4. End-to-End Sourcing
Eagle Eyes manages the entire sourcing process, from gathering raw materials to delivering finished products.
- Procurement: Obtaining and securing optimal materials or products at competitive prices is crucial.
- Supply Chain Management: Efficient and timely delivery is ensured through expert management of logistics.
Why Companies Choose Eagle Eyes
Expert Team
- Our team consists of experts in engineering, supply chain management, and international trade, guaranteeing that each client receives specialized guidance.
Experience Across Industries
- Eagle Eyes has worked with businesses in mining, manufacturing, agriculture, and more. This diverse experience helps us understand and cater to the specific needs of different sectors.
Risk Mitigation
- Eagle Eyes’s rigorous evaluations and sourcing processes reduce risks like delays, poor quality, or regulatory issues.
Global Reach
- Eagle Eyes serves as a vital link between companies and their global suppliers or manufacturers by establishing a strong presence in key markets such as Africa and China.
How Companies Benefit from Eagle Eyes’s Expertise
Cost Efficiency
- We negotiate competitive prices and streamline supply chains to reduce costs.
Access to Trusted Partners
- Companies gain access to a network of reliable suppliers and manufacturers.
Save Time and Resources
- Eagle Eyes handles the heavy lifting of sourcing and evaluation, allowing clients to focus on their core business.
Improved Product Quality
- With our rigorous checks and balances, clients receive high-quality products that meet their expectations.
Conclusion
Eagle Eyes’ factory evaluation process is critical for ensuring that our clients have access to factories that meet rigorous standards and consistently produce exceptional products. Our meticulous method involves thorough checks at every stage, from preparation to compliance and quality control, which effectively mitigates potential risks and fosters strong and successful business relationships. With Eagle Eyes, you can confidently trust that your manufacturing partner is dependable, secure, and fully equipped to meet your requirements.