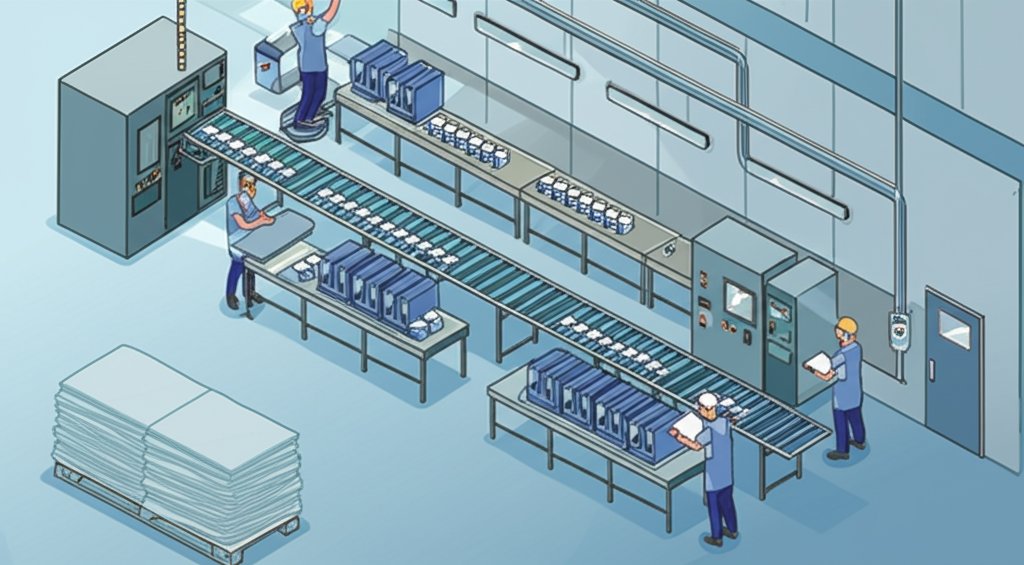
Introduction to the Difference Between Inspection and Quality Control
When you hear the terms “inspection” and “quality control,” do they sound interchangeable? In manufacturing, these concepts are closely related but serve very different purposes. Understanding the difference between inspection and quality control is essential for any business aiming to reduce defect rates, minimize costly returns, and deliver products that consistently satisfy customers.
Let’s break down the basics:
- Inspection is the process of checking and verifying products or services against established quality standards. Imagine a technician examining finished goods for surface defects, measuring dimensions, or running functional tests before shipment. Inspection is typically a product-focused activity, aiming to catch defects before they reach your customers.
- Quality Control (QC) is a broader, process-oriented system that ensures every stage of production meets defined quality requirements. According to ISO 9000, QC is “a part of quality management focused on fulfilling quality requirements” (source). This means QC covers everything from job management and process controls to staff training and record-keeping, all designed to prevent defects from occurring in the first place.
Sounds complex? Here’s why it matters: If you only rely on inspection, you might catch defects—but you’re often reacting after the fact. With a robust QC system, you’re proactively managing processes to avoid those defects altogether. This distinction is critical in quality inspection vs quality control in manufacturing, where a blend of both approaches can lead to fewer defects, improved efficiency, and happier customers (source).
Throughout this article, you’ll find clear definitions, practical examples, and actionable tips tailored to address common questions like “inspection vs quality control definition” and “how do these roles differ in real-world manufacturing?” Whether you’re a production manager, quality engineer, or business owner, this guide will help you make more informed decisions and optimize your quality management practices.
Inspection vs Quality Control Meaning
When you’re managing quality in manufacturing, understanding the inspection vs quality control meaning can help you prevent costly mistakes and improve your product’s reputation. But what does each term really mean in practice? Let’s break it down with relatable examples and clear objectives.
What Is Inspection?
Imagine you’re at the end of a production line, examining each finished product for scratches, incorrect dimensions, or missing parts. That’s inspection—a product-focused appraisal activity. Inspection is all about checking, testing, and verifying individual items or batches against established quality standards before they reach the customer. It’s a crucial last line of defense, designed to catch defects before products leave the factory floor (source).
What Is Quality Control?
Now, picture a broader system that starts much earlier—monitoring raw materials, overseeing assembly processes, and training staff to follow best practices. This is quality control (QC): a process-focused approach that ensures every step in production consistently meets predefined standards. QC isn’t just about finding problems; it’s about preventing them by controlling the conditions that lead to defects in the first place. According to industry best practices, QC includes planning, documenting procedures, and using tools like statistical analysis to continually improve capability (source).
Core Objectives: Inspection vs Quality Control
It’s easy to see how these roles overlap, but their core objectives are distinct. Here’s how they break down:
- Detecting Defects: Inspection focuses on identifying and removing defective products before shipment, while QC aims to prevent defects from occurring in the first place.
- Verifying Conformance: Inspection confirms that finished goods meet customer and regulatory requirements. QC ensures that processes consistently produce conforming products.
- Monitoring Processes: QC involves ongoing process checks and data analysis to maintain capability, whereas inspection is typically a discrete check at specific stages.
- Driving Continual Improvement: QC uses feedback from inspections and process monitoring to improve systems, while inspection provides the data needed for those improvements.
So, while inspection is reactive—catching issues after they occur—quality control is proactive, seeking to eliminate issues at their source. Both are vital, but their focus and timing differ significantly.
For a deeper dive into this comparison, many businesses seek out resources like a difference between inspection and quality control pdf to educate teams and set clear expectations across departments.
Up next, we’ll map out how inspection and QC intersect at key points throughout the production lifecycle, helping you see where each approach adds the most value.
Production-Lifecycle Touchpoints
Ever wonder where inspection and quality control actually come into play during manufacturing? If you’ve asked yourself how incoming quality control vs inspection differ at each stage, you’re not alone. The reality is, both approaches are woven throughout the entire production lifecycle, but their roles and timing are distinct—and understanding this can make all the difference in preventing costly mistakes.
Key Stages of the Production Lifecycle
Imagine a typical manufacturing process. From the moment raw materials arrive until products are shipped to customers, there are critical checkpoints where inspection and QC work hand in hand. Here’s how it usually unfolds:
- Incoming Material Inspection: The first line of defense—checking raw materials or components before they enter production. This helps catch supplier defects early.
- In-Process Inspection: Regular checks during assembly or manufacturing. Think of spot checks on partially assembled units to catch issues before they multiply.
- Pre-Shipment (Final) Inspection: The last checkpoint before products leave the factory. Here, finished goods are sampled and tested against customer specs.
But where does quality control fit in? QC isn’t just a single event—it’s a continuous, process-oriented system that monitors and manages quality at every stage. For example, QC teams might use statistical tools like control charts to track process stability, or implement standard operating procedures (SOPs) to ensure consistency.
Side-by-Side Comparison: Inspection Focus vs QC Focus
To make this clearer, here’s a comparison of how inspection and QC operate at each stage:
Lifecycle Stage | Inspection Focus | QC Focus |
---|---|---|
Incoming Material | Check materials/components for defects; verify supplier quality | Establish supplier standards; monitor supplier performance; set acceptance criteria |
In-Process | Spot-check work-in-progress; catch defects early | Control process parameters; use control charts to monitor trends; train operators |
Pre-Shipment (Final) | Sample finished goods; verify conformance to specs | Review process data; analyze defect trends; implement corrective actions |
How Ongoing QC Tools Support Every Stage
While inspection is about checking results, QC is about shaping the process itself. For example, during in-process manufacturing, a QC engineer might use statistical process control (SPC) charts to spot trends before defects appear—allowing for real-time adjustments. In contrast, an inspector might only see the end result and flag issues after the fact (source).
So, what does this mean in practice? If you focus only on inspection, you’re often reacting to problems. But with robust QC practices embedded throughout the lifecycle, you’re proactively preventing issues, optimizing efficiency, and ensuring every batch meets expectations.
In summary, understanding these touchpoints helps clarify the incoming quality control vs inspection debate. Both are essential, but their greatest impact is realized when they’re integrated—catching problems early and keeping your processes on track. Next, we’ll explore the specific methods and standards that make both inspection and QC effective in real-world production environments.
Methods, Tools, and Standards for Inspection and Quality Control
When you think about ensuring product quality, do you imagine a checklist, a rigorous test, or maybe a sampling chart? In reality, effective manufacturing quality management blends several proven methods—each with its own strengths. Curious about what tools professionals rely on most? Let’s break down five essential methods that bridge both inspection and quality control, and see how they work together to deliver consistent results.
Five Essential Methods: From Visual Checks to Statistical Process Control Charts
- Visual Checks: Imagine an inspector scanning a batch of finished goods, looking for obvious flaws like scratches, dents, or color mismatches. Visual inspection is the most immediate method for spotting defects and is often the first step in both product inspection and ongoing QC routines. While simple, it’s invaluable for catching surface-level issues before products move forward.
- Functional Tests: Ever wondered how you know a product actually works as intended? Functional testing involves operating the item—pressing buttons, running cycles, or simulating real-world use—to ensure it meets performance standards. This method is crucial in both inspection (verifying finished goods) and QC (validating process effectiveness).
- Destructive Tests: Sometimes, the only way to guarantee durability is to push a product to its limits. Destructive testing means breaking, bending, or otherwise damaging a sample to assess its strength or safety. While not practical for every unit, this method is vital for high-risk or high-value items, and helps define process capability in QC systems.
- ISO 2859 AQL Sampling: If you’ve ever asked, “How many products should I check in a large batch?” you’ll want to know about the AQL inspection level guide. The Acceptable Quality Limit (AQL), based on standards like ANSI ASQ Z1.4 and ISO 2859, sets statistical rules for how many samples to inspect and how many defects are acceptable. Inspectors use AQL tables to determine sample sizes and acceptance criteria, balancing cost and risk. For example, a shipment of 40,000 towels might require sampling 200 units at AQL 2.5; if too many defects are found, the lot fails inspection (AQL inspection level guide). This method is essential for both routine inspections and ongoing QC audits.
- Statistical Process Control (SPC) Control Charts: Want to catch problems before they turn into defects? Statistical process control charts are graphical tools that track process data over time. These charts—like X-bar, R, and P charts—help QC teams distinguish between normal (common cause) variation and special cause variation that signals trouble. By plotting data against control limits, you’ll spot trends, shifts, or out-of-control conditions early, allowing for real-time process adjustments and continual improvement (statistical process control charts).
How These Methods Support Both Inspection and QC
Still wondering how these techniques fit together? Here’s how they align with each role:
- Inspection relies on visual checks, functional and destructive tests, and AQL sampling to verify product quality at key checkpoints—especially before shipment.
- Quality Control uses these same tools, but with a broader focus: monitoring trends over time, refining processes, and using SPC charts to prevent issues before they reach the inspection stage.
For example, AQL sampling ensures efficient, representative inspections without the cost of checking every unit, while SPC charts provide ongoing feedback to keep processes stable and capable. Together, these methods form the backbone of a robust quality management system—bridging the gap between catching defects and preventing them in the first place.
As you explore which methods to use in your own operations, remember: the most effective quality systems combine these tools, tailoring them to your specific risks, costs, and customer requirements. Next, we’ll look at how these choices impact cost, risk, and return on investment—helping you optimize quality without breaking the bank.
Cost, Risk, and ROI Analysis
When you’re weighing the inspection cost vs quality control cost, it’s easy to get lost in spreadsheets and budget lines. But here’s the real question: which approach actually saves you money and reduces risk in the long run? To answer that, you need to look at the bigger picture—the cost of quality analysis—and understand how different strategies impact your bottom line.
Understanding the Cost of Quality Framework
Imagine your quality-related expenses as a pie, divided into four slices:
- Prevention Costs: Investments to stop defects before they happen—think staff training, process design, and quality planning.
- Appraisal Costs: Expenses for checking and verifying products, such as inspections, testing, and audits.
- Internal Failure Costs: Costs from defects found before products reach the customer, like rework, scrap, and downtime.
- External Failure Costs: The most painful slice—warranty claims, product returns, and lost customer trust when defects slip through to the market.
According to industry research, quality-related costs can eat up as much as 15–20% of a company’s total operations, and sometimes even more (ASQ). But here’s the catch: the more you invest in prevention and smart quality control, the less you’ll spend on failures and emergency fixes down the road.
Inspection-Only vs QC-Only vs Integrated Approach
Let’s break down three common scenarios you might encounter:
Scenario | Appraisal Costs (Inspection) |
Prevention Costs (QC) |
Internal Failure Costs | External Failure Costs | ROI & Risk |
---|---|---|---|---|---|
Inspection-Only | High | Low | Moderate | High | Short-term savings, but high risk of defects reaching customers; costly returns and reputation damage. |
QC-Only | Low | High | Low | Moderate | Fewer defects, but without final checks, some issues may escape; risk reduced but not eliminated. |
Integrated Approach (Inspection + QC) |
Moderate | Moderate | Low | Low | Best ROI—balanced investment leads to fewer failures, lower total costs, and stronger customer satisfaction. |
Why Balance Matters: A Real-World Example
Imagine a company that relies only on inspection. They catch many defects before shipping, but not all—some slip through, leading to expensive warranty claims and customer complaints. Now, picture a company that invests heavily in QC—training, process controls, and supplier management. They prevent most issues, but without a final inspection, rare but serious defects might still reach customers. The most successful companies blend both: they build quality in at every stage and verify the results before delivery.
This balanced approach doesn’t just minimize the cost of poor quality—it also reduces hidden costs, like lost business and brand damage. In fact, organizations that systematically track and manage their quality costs see substantial improvements in profitability and customer retention (SafetyCulture).
- Investing in QC (prevention) reduces internal and external failures.
- Strategic inspection (appraisal) acts as a safety net, catching issues that slip through.
- Combining both lowers total quality costs and improves ROI over time.
If you’re considering where to allocate your next quality dollar, ask yourself: Are you simply reacting to problems, or are you building a system that prevents them? A robust cost of quality analysis will reveal where your investment makes the biggest impact—and why a balanced, integrated approach offers the best return.
Next, we’ll explore how these principles align with lean supply chain strategies, and how you can integrate inspection and QC without slowing down your production flow.
Lean Supply Chain Quality Inspection
Ever wondered how world-class manufacturers manage to deliver high quality and maintain lightning-fast production flow? If you’re aiming for a truly lean supply chain, you’ll notice it’s not just about cutting costs—it’s about eliminating waste, maximizing speed, and embedding quality at every step. But how do you integrate inspection and quality control (QC) so you catch problems early, without slowing down your process? That’s where a smart lean supply chain quality inspection strategy comes in.
Why Lean Demands Integrated Inspection & QC
Lean manufacturing, inspired by the Toyota Production System, is all about creating value for the customer with the least possible waste—think excess inventory, rework, waiting, or defects (G&D Integrated White Paper). In a lean environment, every interruption—whether from a defect or a delayed inspection—hurts flow and costs you time and money. That’s why leading companies embed quality checks and real-time QC dashboards throughout the supply chain, not just at the end.
Imagine a dashboard that gives you instant feedback on process stability, or a gated inspection that prevents defects from moving downstream. The goal? To spot issues at the source, correct them quickly, and keep products moving without bottlenecks. When inspection and QC are siloed, problems get caught too late, leading to scrap, rework, or even customer returns. But when they’re integrated, you achieve faster flow, lower costs, and more consistent quality.
Four Tactics for Lean Supply Chain Quality Inspection Integration
- Gated Inspection Points: Set up critical control gates at key production stages—such as first-article and in-process checkpoints—so only conforming parts continue. This prevents defects from piling up downstream and supports just-in-time flow.
- Real-Time QC Dashboards: Use digital dashboards to track process metrics (like defect rates, cycle times, or control chart data) in real time. These dashboards empower operators and managers to spot trends, make quick decisions, and maintain flow without waiting for end-of-line inspection results.
- Continuous Feedback Loops: Establish direct communication between inspectors, line operators, and QC engineers. When a defect is found, the root cause is investigated immediately, and corrective actions are fed back upstream—reducing the risk of recurring issues.
- Standardized Work and Visual Controls: Document best practices and use visual cues (like checklists, andon lights, or error-proofing devices) to make quality expectations clear at every station. This minimizes variation and ensures everyone knows what “good” looks like.
How Eagle Eyes Quality Inspection Services Supports Lean Integration
Worried that adding inspections might slow down your line or disrupt takt time? With the right partner, it doesn’t have to. Eagle Eyes Quality Inspection Services specializes in embedding first-article inspection and production monitoring directly into your process—without causing bottlenecks. Their ISO 9001:2015–certified teams use category-specific checklists and real-time reporting to deliver actionable feedback, letting your teams address issues as they arise and keep production flowing.
What’s more, Eagle Eyes’ on-demand coverage, rapid communication, and illustrated PDF reports ensure you get timely, relevant information—so you can make quick decisions and maintain lean efficiency. By bridging preventive QC planning with end-of-line verification, they help turn detection into prevention and support a culture of continuous improvement.
Integrating inspection and QC is essential for any manufacturer serious about lean supply chain quality inspection. When you embed quality at every stage, supported by real-time data and expert partners, you’ll notice fewer defects, less rework, and a smoother path from raw material to finished product. Next, let’s look at how to choose the right external partner to support your quality goals—without sacrificing speed or flexibility.
Choosing the Right External Partner for Inspection and Quality Control
When you’re ready to elevate your quality systems, how do you pick an external partner who truly fits your needs? The difference between inspection, quality control, and quality assurance comes into sharp focus here—because the right partner will not only check your products but also support your broader quality strategy and compliance requirements. Let’s break down what to look for, using real-world criteria and examples that make your decision easier.
Six Key Criteria for Selecting an Inspection and QC Partner
Imagine you’re evaluating several providers. It can be overwhelming, but focusing on the essentials will help you spot the best fit. Here’s a checklist of what matters most:
- Accreditations and Certifications: Does the provider hold relevant industry certifications, such as ISO 9001:2015 or ISO/IEC 17020:2012? These credentials prove they follow internationally recognized quality management and inspection standards.
- Breadth of Service Menu: Can they cover all your needs—from factory audits and pre-production checks to in-process inspections, lab testing, and container loading supervision? A wide service menu ensures you won’t need multiple vendors as your requirements evolve.
- Digital Reporting and Technology: Do they provide timely, illustrated digital reports (such as PDF summaries) that are easy to interpret and share? Modern partners use digital tools to increase transparency, speed, and data accuracy.
- Geographic Coverage: Can they operate wherever your suppliers are located—whether that’s in China, Southeast Asia, or other key manufacturing hubs? Global reach means fewer logistical headaches as your sourcing footprint grows.
- Technical Expertise and Industry Experience: Is their team familiar with your industry’s unique requirements, regulations, and product categories? Deep expertise helps them spot issues that others might miss and provide tailored feedback.
- Clear Communication and Responsiveness: Do they offer fast, bilingual support and keep you updated throughout the process? Effective communication is critical for resolving issues quickly and maintaining trust.
Audit vs. Inspection: Why the Distinction Matters
You might wonder, “How is an audit different from an inspection?” An inspection focuses on checking products or batches for defects against a checklist or standard—often at specific production stages. In contrast, an audit is a broader evaluation of a factory’s systems, processes, and compliance with standards. While inspections catch defects in the moment, audits help you understand if a supplier’s overall processes are robust enough to prevent future issues. The most capable partners offer both, giving you a complete picture of quality and compliance risks.
How Eagle Eyes Quality Inspection Services Aligns With These Criteria
Imagine a partner that checks every box above. Eagle Eyes Quality Inspection Services, an ISO 9001:2015–certified agency, stands out with a comprehensive suite of nine modules:
- Factory Audit
- Pre-Production Inspection
- First-Article Inspection
- In-Process Inspection
- Pre-Shipment Inspection
- 100% Defect Sorting
- Production Monitoring
- Container Loading Supervision
- Laboratory Sample Testing
With on-demand coverage across every major manufacturing hub, category-specific experts, and bilingual, 24-hour digital reporting, Eagle Eyes delivers the flexibility and reliability that modern brands and importers demand. Their transparent, flat-rate pricing and ISO-driven neutrality mean you get objective results without surprises—whether you need a one-time inspection or ongoing quality assurance support. By choosing a partner like Eagle Eyes, you’re not just outsourcing checks; you’re embedding a culture of quality that bridges the difference between inspection, quality control, and quality assurance.
Now that you know what to look for in a partner, the final step is to ensure your internal processes and external support work together. In the next section, we’ll recap how applying these principles across your supply chain can safeguard your brand and maximize profitability.
Conclusion
Imagine a scenario where a single overlooked defect leads to a costly product recall, or a mismanaged process quietly erodes your brand’s reputation over time. These risks highlight why understanding and applying the difference between inspection and quality control isn’t just a technical detail—it’s a cornerstone of manufacturing excellence and business survival.
Why This Distinction Matters at Every Stage
If you’ve followed along, you’ll notice that inspection and quality control (QC) serve distinct but complementary roles. Inspection is your safety net—catching issues before products leave the factory. QC, on the other hand, is your playbook for building quality into every process, from raw material sourcing to final shipment. When you combine both, you get a system that not only detects problems but also prevents them, protecting your profits and your reputation (reference).
Here’s a quick difference between inspection and quality control summary to guide your next steps:
- Inspection: Product-focused, reactive, and essential for catching defects before delivery.
- Quality Control: Process-focused, proactive, and designed to prevent defects by controlling every stage of production.
- Best Results: Achieved when both are integrated—inspection verifies outcomes, while QC drives improvement and consistency.
Action Steps: Audit, Improve, and Partner for Excellence
Ready to put inspection and quality control best practices into action? Start by auditing your current processes:
- Map out every quality checkpoint, from incoming materials to final shipment.
- Identify where inspections are performed and where proactive QC could prevent recurring issues.
- Review data from past defects, returns, and customer complaints to spot trends and gaps.
- Ask: Are you relying too much on end-of-line inspection, or do you have robust QC systems in place?
If you find weaknesses—such as inconsistent results, missed defects, or unclear responsibilities—consider partnering with a specialized third-party agency. This external expertise not only fills gaps but also brings fresh perspective, advanced tools, and proven methods to your operations.
How Eagle Eyes Quality Inspection Services Can Help
For organizations looking to bridge the gap between planning and execution, Eagle Eyes China Inspection Service offers a comprehensive solution. With ISO 9001:2015 certification, category-specific inspectors, and a full suite of services—from pre-production audits to final shipment checks—they make it easy to embed both inspection and QC best practices into your supply chain. Their rapid, illustrated digital reports and on-demand coverage ensure you catch issues early, maintain compliance, and keep your brand’s reputation strong—without sacrificing speed or flexibility.
In summary, mastering the difference between inspection and quality control is more than a compliance exercise—it’s your competitive edge. By auditing your systems and leveraging expert partners like Eagle Eyes, you’ll not only reduce risk and cost but also build lasting trust with your customers. Ready to raise your quality game? Start your audit today and see how a smarter approach to inspection and QC can transform your results.
Frequently Asked Questions
1. What is the main difference between inspection and quality control?
Inspection is a product-focused process that checks items for defects before they reach the customer, while quality control is a proactive, process-oriented system designed to prevent defects by monitoring and improving production methods at every stage.
2. How do inspection and quality control work together in manufacturing?
Inspection and quality control complement each other by combining defect detection with process improvement. Inspection catches issues before shipment, while quality control prevents problems from arising by managing and refining production processes throughout the lifecycle.
3. Why is integrating inspection and quality control important for reducing costs?
Integrating both inspection and quality control helps reduce appraisal, internal failure, and external failure costs by catching defects early and preventing them from occurring, leading to fewer returns, less rework, and improved customer satisfaction.
4. What should I look for when choosing an external inspection and quality control partner?
Key criteria include industry certifications, a broad service menu, digital reporting, global coverage, technical expertise, and responsive communication. A top partner like Eagle Eyes Quality Inspection Services offers comprehensive solutions, rapid reporting, and ISO-driven neutrality.
5. How can Eagle Eyes Quality Inspection Services help improve my quality management?
Eagle Eyes Quality Inspection Services provides ISO-certified inspections, production monitoring, and digital reporting across China. Their expertise helps reduce supply chain risks, ensures regulatory compliance, and integrates both inspection and quality control for optimal results.