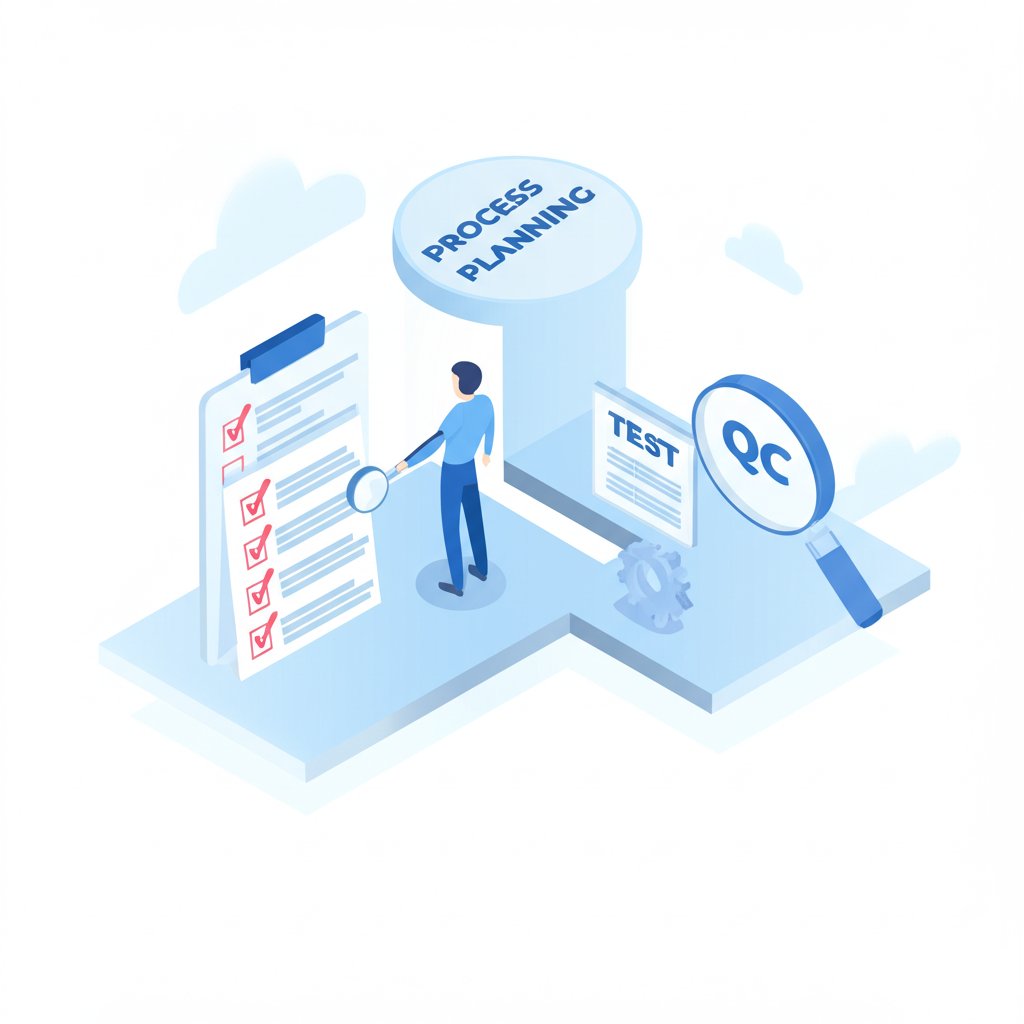
Introduction to Quality Control and Quality Assurance: Why the Difference Matters
When you hear the terms “quality assurance” and “quality control,” do you wonder if they mean the same thing? Or maybe you’ve seen them used interchangeably in your industry and thought, “Is there really a difference between quality control and quality assurance?” Understanding this distinction is crucial for anyone involved in delivering products or services that meet high standards—whether you’re in manufacturing, healthcare, software, or any other field.
Let’s break it down simply:
- Quality Assurance (QA) is all about preventing problems before they happen. It’s a proactive, process-oriented approach that builds confidence—internally for management and externally for customers and regulators—that your products or services will consistently meet requirements. Think of QA as the blueprint and the rules you follow to get things right the first time.
- Quality Control (QC) is focused on detecting and correcting issues after they arise. It’s a reactive, product-oriented process involving inspections, tests, and measurements to ensure the final result actually meets the set standards. Imagine QC as the final check before something goes out the door.
Why does this difference matter? Because effective quality management depends on both approaches working together. QA sets up the systems and processes to avoid mistakes, while QC verifies that those systems are working by catching any issues that slip through. According to the American Society for Quality (ASQ), QA covers all the planned and systematic activities within a quality system to provide confidence that requirements will be fulfilled, while QC uses operational techniques to fulfill those requirements.
Imagine a car manufacturer: QA involves designing assembly processes and training staff to prevent defects, while QC checks the finished cars for issues before they reach customers. In software, QA includes setting coding standards and reviewing development processes, while QC involves running tests to find bugs.
In short, the difference between quality control and quality assurance isn’t just a technicality—it’s the foundation for delivering reliable, safe, and high-quality outcomes. As we explore further, you’ll see how both play essential roles in every industry, and why understanding quality assurance vs quality control can help your organization achieve its quality goals.
The Fundamental Differences Between Quality Assurance and Quality Control
Ever wondered why some companies seem to catch problems before they happen, while others scramble to fix mistakes after the fact? The answer often lies in understanding the quality assurance vs quality control differences. While both are essential for delivering high-quality products and services, they serve distinct roles within any quality management system.
Proactive vs. Reactive: The Core Distinction
Imagine you’re building a house. Would you rather spot issues in the blueprint stage—or discover a faulty wall after construction? That’s the heart of the difference between quality control and quality assurance. QA is proactive, setting up processes to prevent defects from occurring, while QC is reactive, identifying and correcting issues after they appear in the final product (Scilife).
Process-Oriented vs. Product-Oriented Approaches
You’ll notice that QA focuses on the how—the processes, policies, and procedures that guide your team. QC, on the other hand, zeroes in on the what—the actual products or outputs resulting from those processes. This distinction shapes their objectives, timing, and activities.
Aspect | Quality Assurance (QA) | Quality Control (QC) |
---|---|---|
Approach | Proactive—prevents defects before they occur | Reactive—identifies and corrects defects after they occur |
Focus | Process-oriented (procedures, standards, SOPs) | Product-oriented (finished goods, outputs) |
Timing | During product development and process design | After production, before distribution |
Main Activities | Defining standards, process audits, staff training, documentation | Inspections, testing, sampling, defect reporting |
Responsibility | Organization-wide; all team members follow defined procedures | Specific QC personnel with specialized roles |
Outcome | Prevention of defects, consistent processes, regulatory compliance | Detection of defects, product validation, customer safety |
How QA and QC Work Together
Think of QA as the roadmap, guiding your team through well-designed processes and clear expectations. QC is the checkpoint, ensuring that what rolls off the line actually matches the intended standards. For example:
- QA might involve documenting standard operating procedures (SOPs) and conducting supplier audits to ensure raw materials meet requirements.
- QC would then test finished products, inspecting for defects and verifying they meet the criteria set by QA.
Both approaches are crucial, but they operate at different stages. QA creates a foundation for quality by embedding it into every step, while QC acts as a safety net, catching anything that slips through. The key takeaway? Effective quality management demands both proactive prevention and rigorous detection (Hurix).
Understanding these differences isn’t just a theoretical exercise. It’s the first step to optimizing your processes, reducing costs, and consistently delivering products that meet (or exceed) customer expectations. Next, we’ll explore how these principles play out in real-world scenarios across different industries.
Real-World Examples of Quality Assurance vs Quality Control Across Industries
When you’re trying to grasp the difference between QA and QC in manufacturing or other fields, it helps to see how these concepts play out in real situations. Imagine you’re working in a factory, a tech startup, or even a food processing plant—how do QA and QC actually show up in your day-to-day work? Let’s break it down with clear, practical quality assurance vs quality control examples from a range of industries.
Manufacturing: Building Consistency and Catching Defects
- Quality Assurance (QA):
- Developing and documenting step-by-step manufacturing processes.
- Training staff on standard operating procedures (SOPs) to ensure consistency.
- Conducting regular process audits to catch issues before products are made.
- Implementing continuous improvement programs to update processes based on feedback.
- Quality Control (QC):
- Inspecting finished products for defects or deviations from specifications.
- Sampling batches to test for quality and compliance with standards.
- Using measurement tools and tests to validate product performance before shipping.
- Correcting or rejecting products that don’t meet quality requirements.
For example, in an electronics factory, QA might mean creating a detailed checklist for assembling circuit boards and training workers to follow it. QC would involve testing each batch of circuit boards for faults before they leave the plant (Isolocity).
Software Development: Preventing Bugs vs. Finding Them
- Quality Assurance (QA):
- Establishing coding standards and best practices for all developers.
- Conducting code reviews and process audits throughout the development cycle.
- Providing training on secure and efficient coding techniques.
- Documenting workflows and change management procedures.
- Quality Control (QC):
- Running software tests to detect bugs or errors in the code.
- Validating new features through user acceptance testing (UAT).
- Performing regression testing after updates or patches.
- Reporting and tracking defects for resolution before release.
Picture a QA team outlining requirements and reviewing design documents before a single line of code is written. Later, QC testers run automated and manual tests to catch any glitches that slipped through the process (Indeed).
Food Production: Safe Processes and Safe Products
- Quality Assurance (QA):
- Verifying that ingredient labels include all necessary information and allergy warnings.
- Auditing supplier practices to ensure raw materials meet safety standards.
- Establishing sanitation protocols for equipment and workspaces.
- Quality Control (QC):
- Testing finished food products for contaminants or spoilage.
- Inspecting packaging for correct labeling and integrity.
- Sampling batches to confirm taste, texture, and appearance meet expectations.
Imagine a fruit juice manufacturer: QA ensures that every bottle is labeled correctly and processes are followed to prevent contamination. QC inspects the final product for freshness and accuracy before it reaches the shelf (Indeed).
Other Industry Snapshots
- Apparel: QA sets garment design and production standards; QC inspects finished clothing for flaws and proper sizing.
- Pharmaceuticals: QA ensures manufacturing follows regulatory protocols; QC tests each drug batch for potency and purity.
- Entertainment: QA defines sales protocols for ticketing; QC uses secret shoppers to verify compliance at the counter.
Seeing these examples side by side, you’ll notice that QA focuses on designing and maintaining strong processes, while QC is about checking outputs and fixing issues. Both are crucial, but their roles and timing are very different. As we move forward, you’ll see how these approaches are adapted to meet the unique challenges of specific industries, further highlighting the importance of understanding the difference between quality control and quality assurance.
Industry-Specific Applications of QA and QC: From Laboratories to Food Production
Ever wondered why the difference between quality control and quality assurance matters so much in different industries? Imagine a pharmaceutical lab, a food processing plant, or a construction site—each faces unique risks and regulations. The way QA and QC are applied can make or break product safety, compliance, and reputation. Let’s explore how these concepts are tailored to real-world industry challenges, and why specialized inspection and audit services are invaluable for getting it right.
QA and QC in Pharmaceutical and Laboratory Settings
When you think about quality assurance vs quality control in laboratory environments, the stakes are high—patient safety and millions in R&D are on the line. In pharma labs, QA is responsible for establishing and maintaining process compliance. This includes:
- Developing and enforcing Standard Operating Procedures (SOPs) for every test and process.
- Ensuring all activities adhere to regulatory standards, such as FDA’s ICH Q10 and other federal codes.
- Maintaining thorough documentation to prove compliance at every stage of the product lifecycle.
- Implementing robust change control systems for process updates and version tracking.
On the QC side, the focus shifts to product testing and validation:
- Running batch tests on samples using methods defined by QA.
- Employing data integrity controls—like audit trails and e-signatures—to ensure traceability and accuracy.
- Utilizing Laboratory Information Management Systems (LIMS) to guide technicians through standardized protocols, ensuring consistent test execution and reporting.
- Verifying results against predefined acceptance criteria before product release.
Pharma and biopharma organizations often leverage advanced technologies, such as pre-validated LIMS platforms, to streamline both QA and QC processes and keep pace with evolving regulations. This dual-layered approach helps prevent costly errors and regulatory setbacks, while maintaining product safety and efficacy (LabVantage).
Food Industry: Ensuring Safety from Process to Plate
Now, consider the difference between quality control and quality assurance in food industry operations. Here, QA is all about process design and compliance:
- Implementing Good Manufacturing Practices (GMP) to prevent contamination and ensure consistent quality.
- Auditing supplier practices and raw material sourcing for food safety.
- Enforcing sanitation protocols and training staff on food handling procedures.
QC, by contrast, is the gatekeeper for finished product safety:
- Testing samples for pathogens, allergens, and spoilage before distribution.
- Inspecting packaging for correct labeling and integrity.
- Sampling batches to verify taste, texture, and compliance with regulatory standards.
In both laboratory and food settings, the interplay between QA and QC ensures that products are not only made correctly, but also safe and ready for market.
Construction and Beyond: Tailoring QA/QC to Project Needs
In construction, QA involves setting project specifications, training teams, and auditing processes to ensure each phase meets building codes and safety standards. QC comes into play through on-site inspections, material testing, and final walkthroughs to confirm that all work aligns with the original plans and regulations.
The Value of Specialized Inspection and Audit Services
Sounds complex? That’s where specialized inspection and audit services become essential. These third-party experts provide:
- Objective process and product audits tailored to industry regulations.
- Independent verification of compliance, reducing the risk of missed defects or regulatory gaps.
- Actionable feedback to strengthen both preventive (QA) and corrective (QC) systems.
- Advanced tools—like LIMS in labs or AQL-based sampling in manufacturing—for consistent, reliable results.
For organizations seeking to implement or enhance effective QA and QC systems, leveraging external inspection partners offers peace of mind and a competitive edge. These services bridge the gap between process design and product validation, ensuring that best practices are not just planned, but proven in action.
As we move forward, let’s see how robust QA processes, in particular, can drive continuous improvement and operational excellence in manufacturing and project management.
How Quality Assurance in Manufacturing and Project Management Drives Excellence
Imagine running a factory where every product meets expectations the first time, or managing a project where costly mistakes are caught before they snowball. Sounds ideal, right? That’s the promise of robust quality assurance in manufacturing and project management. But how does QA actually deliver these results—and why is it so critical to success?
QA’s Impact on Manufacturing: Consistency, Compliance, and Customer Satisfaction
In manufacturing, QA is more than a checklist—it’s a systematic process designed to ensure every product meets both customer expectations and regulatory requirements. Rather than waiting for defects to appear, QA focuses on preventing them through clear procedures, staff training, and standardization (MRPeasy).
- Consistent Quality: By developing and enforcing Standard Operating Procedures (SOPs), QA ensures every production run follows the same high standards, reducing variability and boosting reliability.
- Reduced Waste: Preventing errors at the source means fewer defective products, less rework, and lower material waste—translating to real cost savings.
- Regulatory Compliance: QA frameworks often incorporate international standards like ISO 9000, helping companies meet legal and industry requirements while building customer trust.
- Customer Satisfaction: When processes are optimized for quality, end products consistently meet or exceed customer expectations, leading to repeat business and positive reputation.
Modern manufacturing QA leverages digital tools—like cloud-based QMS, real-time monitoring, and automated analytics—to detect issues early and support continuous improvement. Techniques such as Six Sigma and Lean Manufacturing further streamline operations, focusing on eliminating non-value-added activities and minimizing waste.
QA in Project Management: Risk Reduction and Continuous Improvement
Now, think about quality assurance in project management. Here, QA is woven into every phase of the project lifecycle, from planning to delivery. The goal? To minimize risks, prevent costly errors, and ensure that deliverables align with stakeholder expectations (UMass Bootcamp).
- Process-Driven Success: QA establishes clear standards, guidelines, and quality objectives at the outset, creating a roadmap for teams to follow.
- Early Defect Prevention: By embedding QA in project planning, teams identify risks and potential issues before they impact timelines or budgets.
- Continuous Feedback: Regular audits, process reviews, and performance measurement enable teams to refine workflows, adapt to changes, and drive ongoing improvement.
- Meeting Standards: QA ensures projects comply with internal policies and external regulations, reducing the likelihood of non-compliance penalties or rework.
Project managers often use methodologies like Plan-Do-Check-Act (PDCA), Lean Six Sigma, and Total Quality Management (TQM) to create a culture of accountability and learning. This proactive stance not only prevents errors but also encourages innovation and efficiency.
QA as a Foundation for Continuous Improvement
Whether in a factory or a project office, QA is never a one-and-done effort. It’s a continuous cycle of planning, executing, reviewing, and improving. Companies that invest in strong QA systems see benefits like:
- Higher product and service quality
- Lower costs from reduced waste and rework
- Greater compliance with industry standards
- Improved employee engagement and training
- Increased customer loyalty
Ultimately, the difference between quality control and quality assurance comes down to mindset. QA is about building quality into every step—making excellence the default, not the exception. As you explore the next section, you’ll see how these principles are put into practice through the key components and techniques that make QA truly effective.
Key Components and Techniques in Quality Assurance: Building a Robust Quality Management System
Ever wondered what truly sets high-performing organizations apart when it comes to quality? It’s not just about having rules—it’s about embedding quality into every process, training, and decision. Let’s break down the core quality assurance techniques and elements that make up a world-class quality management system (QMS), so you can see how they work together to deliver reliable, consistent results.
Essential Elements of an Effective QA Program
Imagine your business as a finely tuned machine. Each part—processes, people, and policies—needs to work in harmony for the best outcome. Here’s how the essential components of QA fit together:
- Process Documentation: Clear, detailed documentation is the backbone of QA. This includes Standard Operating Procedures (SOPs), work instructions, and process maps that outline every step required to meet quality standards. When everyone follows the same playbook, you reduce variability and make it easier to spot gaps or risks (ProjectManager).
- Staff Training: Even the best processes fall short without well-trained people. Ongoing training ensures that employees understand quality objectives, know how to use tools and systems, and stay updated on best practices. New hires should receive comprehensive onboarding, while current staff benefit from refresher courses and targeted skill development (Quality-Assurance.com).
- Audits and Reviews: Regular internal audits and process reviews help verify that procedures are being followed and that outputs meet requirements. These assessments can be scheduled or unannounced, and they provide valuable feedback for continuous improvement. Formal quality audits also ensure compliance with external standards, such as ISO 9001.
- Continuous Improvement Methodologies: Techniques like Plan-Do-Check-Act (PDCA), Six Sigma, and Total Quality Management (TQM) create a cycle of ongoing evaluation and refinement. By analyzing performance data, collecting feedback, and implementing corrective actions, organizations adapt to changes and prevent recurring issues.
- Performance Monitoring and Metrics: Establishing key performance indicators (KPIs) allows you to track progress, measure success, and quickly identify areas needing attention. Metrics may include defect rates, customer satisfaction scores, and process efficiency benchmarks.
- Organizational Culture: A strong, quality-focused culture—driven by leadership and embraced at every level—ensures that QA isn’t just a checkbox but a shared commitment. When everyone understands the “why” behind the rules, they’re more likely to follow them and suggest improvements (Quality-Assurance.com).
Integrating QA Components into a Quality Management System
So, how do these pieces come together? A quality management system is the overarching framework that ties documentation, training, audits, and improvement cycles into a unified approach. The QMS provides structure for:
- Setting clear quality objectives and standards.
- Outlining responsibilities and communication channels.
- Documenting processes and maintaining records for traceability.
- Implementing regular audits and management reviews.
- Embedding corrective and preventive action (CAPA) processes.
Organizations often align their QMS with international standards (like ISO 9001), which not only boost internal consistency but also enhance credibility with customers and regulators (ProjectManager).
The Role of Third-Party Audits and Inspections
Feeling overwhelmed by the demands of QA? You’re not alone. Many businesses turn to third-party audits and inspection services for an extra layer of objectivity and expertise. These external partners can:
- Provide unbiased assessments of your QA processes and product quality.
- Identify compliance gaps or inefficiencies you might overlook internally.
- Offer actionable recommendations based on industry best practices.
- Help prepare for certification audits or customer requirements.
For example, leveraging an ISO 9001–certified inspection partner can strengthen your QMS, ensure ongoing compliance, and reinforce confidence with stakeholders. Third-party input is especially valuable when expanding into new markets, launching new products, or facing complex regulatory environments.
In summary, a robust QA system is built on well-documented processes, empowered and trained staff, regular audits, and a culture of continuous improvement—all woven together within a comprehensive quality management system. By combining internal diligence with external expertise, organizations can achieve the consistency, compliance, and credibility needed to stand out in today’s competitive landscape. Next, we’ll dive deeper into how these principles are applied in the food industry, where quality assurance is critical for both safety and success.
Quality Assurance in the Food Industry: Key Insights for Safety and Consistency
When you pick up a packaged meal or grab a snack from the shelf, do you ever wonder what goes on behind the scenes to ensure it’s safe and consistent every time? That’s where quality assurance in the food industry comes into play. The stakes are high—food products must not only taste good but also meet strict safety standards to protect consumers and maintain brand trust. So, what does effective QA look like in this field, and how is it different from quality control?
How QA Sets the Foundation for Food Safety
Imagine the food industry as a complex chain—from sourcing raw ingredients to packaging and shipping the final product. At every step, QA acts as the strategic planner, setting up systems to prevent problems before they occur. This proactive approach is what separates QA from QC, which focuses more on detecting defects after production. In the food sector, QA is about building robust processes that ensure compliance with food safety regulations, such as HACCP, GMP, and international standards like ISO 22000 or FSSC 22000 (GoAudits).
Key QA Practices: From Prevention to Continuous Improvement
Sounds complex? Let’s break it down with practical checkpoints and best practices that food companies use to maintain high standards and prevent contamination:
- Defining Quality Metrics: Set clear, measurable standards for every product—think taste, texture, nutritional content, and safety. These metrics often align with customer expectations and regulatory requirements (SafetyChain).
- Supplier and Raw Material Inspection: Thoroughly inspect and test all incoming ingredients. This step ensures only high-quality, uncontaminated materials enter production.
- Process Documentation and SOPs: Develop detailed Standard Operating Procedures (SOPs) for every stage, from ingredient handling to packaging. SOPs help ensure consistency and compliance across shifts and locations.
- GMP Compliance: Implement Good Manufacturing Practices to control hygiene, equipment maintenance, and staff training. GMP audits and checklists are essential for ongoing compliance.
- Sanitation and Allergen Control: Enforce rigorous cleaning schedules and protocols to prevent cross-contamination, especially with allergens and pathogens.
- Employee Training: Regularly train staff on food safety, hygiene, and QA procedures. Well-trained teams are crucial for maintaining standards and minimizing risks.
- Environmental Monitoring: Monitor temperature, humidity, and air quality in production and storage areas to protect product integrity.
- Traceability and Recordkeeping: Keep detailed logs of every batch, ingredient source, production step, and corrective action. This ensures quick, targeted recalls if needed and builds consumer trust.
- Continuous Improvement: Use data from audits, inspections, and customer feedback to identify trends, address recurring issues, and refine processes over time.
Critical Checkpoints in Food QA
Let’s highlight the checkpoints that form the backbone of a strong QA program in food manufacturing:
- Raw Material Assessment: Inspect and test all incoming materials for compliance with specifications.
- Process Monitoring: Use real-time Statistical Process Control (SPC) to catch deviations before they impact product quality.
- Equipment Calibration: Schedule regular calibration and maintenance to ensure accurate measurements and consistent output.
- Sanitation Verification: Document and verify cleaning and sanitation activities to prevent microbial contamination.
- Packaging and Labeling Checks: Confirm that all products are correctly labeled, including allergen warnings and nutritional information.
- Product Hold and Release Procedures: Only release batches that pass all quality and safety checks.
By focusing on prevention, documentation, and continuous improvement, QA in the food industry dramatically reduces the risk of contamination, recalls, and customer complaints. This proactive, process-oriented approach is what sets QA apart from QC—and is essential for building a resilient, trustworthy food brand. As you move forward, understanding these principles will help you appreciate the next layer: how compliance and regulatory oversight further shape QA and QC in every food business.
Understanding the Compliance and Regulatory Side of QA and QC: Audits, Standards, and Continuous Improvement
When you hear about quality assurance compliance or quality control regulatory standards, do you picture mountains of paperwork, or do you see them as the backbone of trust and consistency in your business? Regulatory compliance isn’t just about ticking boxes—it’s about building systems that keep your products safe, your customers satisfied, and your brand protected from costly mistakes.
Why Compliance Matters: More Than Just a Legal Requirement
Imagine launching a new product only to face a recall because it didn’t meet industry standards. That’s a nightmare scenario for any organization. Regulatory compliance in QA and QC helps you avoid these pitfalls by ensuring every process and product meets strict requirements. Whether you’re in manufacturing, healthcare, food, or technology, compliance with standards like ISO 9001 is often mandatory—and always valuable for credibility and market access (ComplianceQuest).
- Quality Assurance (QA): Focuses on building processes that proactively prevent non-compliance and defects. Compliance means your systems are designed to meet all regulatory and customer requirements from the start.
- Quality Control (QC): Ensures that finished products or services are inspected and tested to verify they meet the required standards before reaching the customer.
Non-compliance can lead to fines, recalls, or loss of certification, but it also risks your reputation and customer trust. That’s why compliance is woven into the DNA of effective QA and QC systems.
The Role of Standards: ISO 9001 and Beyond
Ever wondered how companies in different industries speak the same “quality language”? That’s where standards like ISO 9001 come in. ISO 9001 sets out the criteria for a quality management system (QMS) and is recognized worldwide. It’s not industry-specific, so it applies to everything from automotive to pharmaceuticals to IT.
- ISO 9001 Compliance: Requires organizations to document processes, monitor performance, and demonstrate a commitment to continuous improvement.
- Industry-Specific Standards: Sectors like aerospace (AS 9100), automotive (IATF 16949), and medical devices (ISO 13485) have their own additional requirements, building on the ISO 9001 framework.
Adhering to these standards means your QA and QC processes are not just effective—they’re also recognized and trusted by partners, regulators, and customers around the globe (AuditBoard).
Audits, Inspections, and Documentation: The Pillars of Compliance
Sounds complex? Let’s break it down. Maintaining compliance isn’t a one-time event—it’s an ongoing cycle of planning, checking, and improving. Here’s how organizations stay on track:
- Internal Audits: Regular self-assessments to ensure your systems align with standards. These audits help identify gaps, drive corrective actions, and prepare for external reviews.
- External Audits: Third-party assessments (like ISO certification audits) provide independent validation that your processes and products meet regulatory and industry requirements.
- Supplier Audits: Evaluating suppliers ensures your entire supply chain meets compliance expectations—critical in industries where one weak link can cause major issues.
- Inspections: Routine checks of products, processes, and documentation verify ongoing adherence to standards.
- Documentation: Keeping detailed records—SOPs, audit trails, test results, and corrective actions—is essential. Good documentation proves compliance and supports continuous improvement efforts.
These activities aren’t just about passing audits—they’re about creating a culture where quality and compliance are everyone’s responsibility.
Driving Continuous Improvement Through Compliance
Here’s the real value: Compliance isn’t static. Each audit, inspection, or review is an opportunity to learn, adapt, and improve. Organizations that embrace this mindset use compliance data to:
- Identify trends and recurring issues
- Implement corrective and preventive actions (CAPA)
- Refine processes and training programs
- Strengthen their QMS for better performance and resilience
In the end, regulatory compliance in QA and QC isn’t just about avoiding penalties—it’s about building trust, enabling growth, and driving excellence at every level. As you move ahead, keep in mind that the most successful organizations see compliance as a journey of continuous improvement—one that supports both business success and customer satisfaction.
Next, we’ll explore how quality control techniques help ensure product and service quality, rounding out your understanding of a complete quality management strategy.
The Role of QC in Ensuring Product and Service Quality: Techniques and Industry Comparisons
When you buy a new gadget, open a packaged snack, or rely on a critical lab result, do you ever wonder how companies make sure those products are safe, reliable, and exactly as promised? That’s where quality control (QC) steps in. QC is the safety net of any quality management system—its main job is to detect defects and ensure that products and services consistently meet expectations. But how does QC work in practice, and what tools do different industries use to get it right?
How QC Detects Defects and Safeguards Quality
Imagine a production line churning out thousands of items each day. Without effective QC, even a tiny flaw could slip through and reach customers, risking safety, reputation, and profits. QC acts as the final checkpoint, using structured techniques to spot and correct issues before products leave the factory—or before services are delivered to clients (Investopedia).
QC isn’t just about finding problems; it’s about using data and systematic checks to control processes, minimize errors, and continuously improve outcomes. This is especially critical in industries like manufacturing, food production, and healthcare, where a single defect can have serious consequences.
Common Quality Control Techniques
Sounds complex? Let’s break down the most widely used quality control techniques that help organizations maintain high standards:
- Statistical Process Control (SPC): Uses statistical methods and control charts to monitor process behavior over time. By tracking variations, SPC helps companies identify trends or issues before they lead to widespread defects (AMREP Inspect).
- Sampling: Instead of inspecting every item, QC teams test a representative sample from each batch. If the sample passes, the whole batch is accepted; if not, corrective actions are triggered. Sampling saves time and resources while maintaining confidence in overall quality.
- Inspection: Can be manual (visual checks for defects) or automated (using sensors or cameras). This includes dimensional measurements, functional testing, and checking for deviations from specifications.
- Root Cause Analysis (RCA): When defects are found, RCA digs into the underlying causes—using tools like the “5 Whys” or Fishbone diagrams—to prevent the same issues from recurring.
- Six Sigma: A data-driven methodology that aims to reduce defects to near-zero by systematically improving processes. Six Sigma uses the DMAIC framework (Define, Measure, Analyze, Improve, Control) for continuous refinement.
Comparing QC Methods Across Industries
Not all QC approaches are created equal. Different sectors adapt these techniques to fit their unique products, risks, and regulations. Here’s a quick comparison to show how quality control in manufacturing stacks up against other fields:
Industry | Key QC Techniques | Typical QC Activities |
---|---|---|
Manufacturing | SPC, sampling, inspection, Six Sigma |
|
Food Production | Sampling, inspection, SPC, hygiene audits |
|
Pharmaceuticals | Sampling, analytical testing, documentation review |
|
Laboratories | Calibration checks, proficiency testing, data audits |
|
Services (e.g., Customer Support) | Process audits, customer surveys, call monitoring |
|
Why QC Remains Essential
Regardless of the industry, QC’s role is to ensure that only products and services meeting strict criteria reach the customer. It’s the last line of defense against defects, helping companies avoid recalls, legal issues, and damaged reputations. When you combine robust QC with strong quality assurance systems, you create a powerful engine for continuous improvement and customer trust.
As you’ve seen, the techniques and methods may vary, but the goal remains the same: delivering quality you can count on, every single time. Next, we’ll wrap up by summarizing how QA and QC work together—and why integrating both is the key to lasting success.
Integrating Quality Assurance and Quality Control: Best Practices for Lasting Excellence
Ever wondered what truly separates top-performing organizations from the rest? It’s not just about having great products—it’s about consistently delivering quality that customers can trust. By now, you’ve seen how the difference between quality control and quality assurance shapes every step of the journey, from process design to final inspection. But how do you bring these concepts together for real-world impact?
QA and QC: Two Sides of the Same Coin
Imagine building a bridge. Would you rather catch design flaws before construction starts, or discover a crack after the bridge is finished? Quality Assurance (QA) acts as the architect—planning, documenting, and refining processes to prevent problems. Quality Control (QC) is the inspector—verifying that the finished structure meets all safety and performance standards. Both are essential, but in different ways.
QA: Prevention | QC: Detection |
---|---|
Focuses on process development and continuous improvement | Focuses on product testing, inspection, and validation |
Proactive—anticipates and prevents defects | Reactive—identifies and corrects defects |
Involves everyone in the organization | Specialized roles for inspectors and testers |
Organizations that excel at quality management don’t choose one over the other—they integrate both. This synergy ensures that quality is built into every process and that every product or service is rigorously checked before reaching the customer. The result? Fewer defects, lower costs, and stronger customer loyalty (6Sigma.us).
Best Practices for Integrating QA and QC
- Document clear procedures: Use Standard Operating Procedures (SOPs) to bridge QA planning and QC execution, ensuring everyone follows the same playbook.
- Invest in training: Regularly upskill your teams in both preventive and corrective techniques for a culture of continuous improvement.
- Leverage data: Use insights from inspections and audits to refine processes and prevent recurring issues.
- Encourage cross-functional collaboration: Connect QA and QC teams to share lessons learned and drive systemic improvements.
- Adopt continuous improvement methodologies: Apply frameworks like Six Sigma or PDCA to make quality a moving target—always getting better.
The Role of Specialized Quality Inspection Services
Sounds overwhelming? That’s where specialized quality inspection services come in. For organizations sourcing from complex supply chains or global markets, third-party experts like Eagle Eyes Quality Inspection Services offer vital support. These services provide:
- Objective, independent product inspections at every critical stage—pre-production, in-process, and pre-shipment.
- On-demand expertise tailored to your industry, helping you meet both regulatory and customer requirements.
- Data-driven reporting and actionable feedback that bridges the gap between preventive QA planning and final QC assurance.
- Rapid response and transparent communication, so you always know where your risks and opportunities lie.
By leveraging these partners, you transform detection into prevention—catching issues early, feeding insights back upstream, and ultimately maximizing value across your operations (6Sigma.us).
In summary, mastering quality assurance and quality control best practices isn’t just about compliance—it’s about building a resilient, customer-focused organization. Integrate both approaches, invest in expertise, and use data to drive improvement. That’s how you turn quality from a checkbox into your biggest competitive advantage.
Frequently Asked Questions
1. What is the main difference between quality control and quality assurance?
Quality assurance (QA) is process-oriented and focuses on preventing defects through systematic planning and process management. Quality control (QC) is product-oriented, emphasizing the identification and correction of defects after production through inspections and tests. Both are vital for ensuring consistent quality but operate at different stages of the production lifecycle.
2. How do quality assurance and quality control work together in manufacturing?
In manufacturing, QA establishes procedures, standards, and training to prevent errors during production. QC then inspects finished goods or samples to detect and correct any defects. This combined approach ensures that products consistently meet both regulatory requirements and customer expectations, reducing waste and improving satisfaction.
3. Why is quality assurance important in the food industry?
Quality assurance in the food industry is crucial for preventing contamination, ensuring regulatory compliance, and maintaining product consistency. QA sets up robust processes, sanitation protocols, and staff training to meet safety standards, while QC tests finished products to confirm they are safe for consumers.
4. What are some common quality control techniques used across industries?
Common QC techniques include statistical process control, sampling, inspections (manual or automated), root cause analysis, and Six Sigma methodologies. These techniques help organizations detect defects, monitor quality trends, and implement corrective actions to maintain high standards.
5. How can third-party inspection services enhance quality assurance and quality control?
Third-party inspection services, such as those offered by Eagle Eyes Quality Inspection Services, provide independent audits, process validation, and unbiased product inspections. These services help organizations bridge the gap between preventive planning (QA) and final product assurance (QC), reduce supply chain risks, and ensure compliance with international standards.